Understanding the Principles Behind MEMS Pirani Vacuum Gauges and Sensors
A MEMS Pirani vacuum sensor, gauge or transducer is a device for measuring vacuum gas pressure by measurement of the pressure dependent heat-loss from a heated resistive element deposited on a suspended micro-machined diaphragm. The MEMS Pirani vacuum transducer can measure vacuum gas pressure over a span of 9 decades from atmospheric pressure down to 1.0E-6 mbar (7.5E-7 Torr).
A micro-electro-mechanical system (MEMS) sensor can be made by traditional semiconductor fabrications techniques such as lithography, etching, annealing and deposition of materials using vapor deposition processes. Silicon can be used as base wafer material for MEMS sensor devices and is also the preferred material for MEMS Pirani sensors.
A micro-electro-mechanical system (MEMS) sensor can be made using traditional semiconductor fabrication techniques such as lithography, etching, annealing, and the deposition of materials through vapor deposition processes. Silicon is often used as the base wafer material for MEMS sensor devices and is also the preferred material for MEMS Pirani sensors.
MEMS Pirani gauges and sensors are also commonly referred to as micro-Pirani gauges or sensors.
The first commercially available vacuum gauge based on MEMS Pirani sensor technology was introduced in 1993 by the Danish technology company Wenzel Instruments. In 2003, Wenzel Instruments was acquired by MKS Instruments Inc., and the Wenzel MEMS Pirani vacuum gauge product line was continued under the MKS brand. MEMS Pirani gauges and transducers have been used for decades, proving their advantages in various applications in the semiconductor industry, analytical equipment, and coating industry.
The traditional Pirani gauge, invented in 1906 by Marcello S. Pirani, consists of a thin resistive metal wire suspended in a tube. The wire Pirani sensor can be operated in a balanced Wheatstone bridge circuit, where one of the legs in the bridge circuit is the resistive sensor wire, while the other legs serve as temperature compensation and balancing. In the balanced bridge configuration the power to the sensor filament is regulated by a controller to keep sensor wire at a fixed target temperature.
The Pirani gauge was invented and first published in 1906 by Marcello Stefano Pirani. The invention of the Pirani gauge was a classic example of experiencing a problem and then finding an innovative solution to that problem.
MEMS Pirani Design
The MEMS Pirani sensor is based on a resistive element deposited on an ultra-thin diaphragm (5) suspended in the vacuum where the gas pressure is measured. The diaphragm is permanently mechanically fixed and does not bend or move with changes in vacuum gas pressure. The resistive element (1) is made of a material with a high temperature coefficient, like nickel.
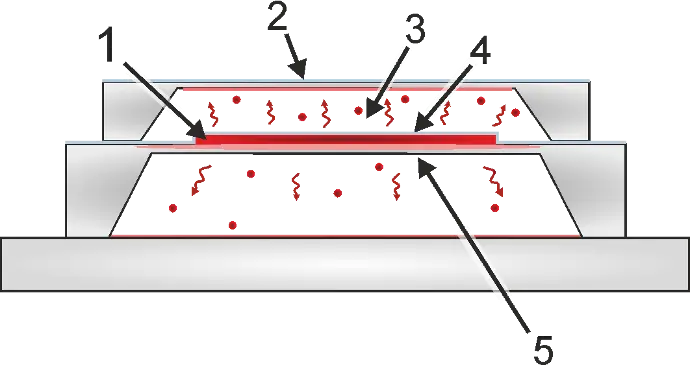
When an electrical current flows through the resistive element, heat is generated by Joule heating, also commonly referred to as resistive heating or ohmic heating. The power deposited in the resistive sensor element must be adequate to heat the sensor element, ensuring effective emissivity to the surrounding gas for measurement of pressure by heat-loss. Compared to the power deposited in a wire Pirani sensor element, the power required to operate a MEMS Pirani resistive element is significantly lower, typically in the microwatt range.
A cavity (3) is formed above the resistive sensor element, which acts as a heat sink to increase the measurement sensitivity at higher pressures where the mean free path of the gas molecules becomes smaller than the distance between the filament and the heat sink. Gas is passed to the cavity by diffusion only, not by flow, due to the geometry of the sensor. The resistive sensor element is protected by a Silicon Nitride passivation layer (4).
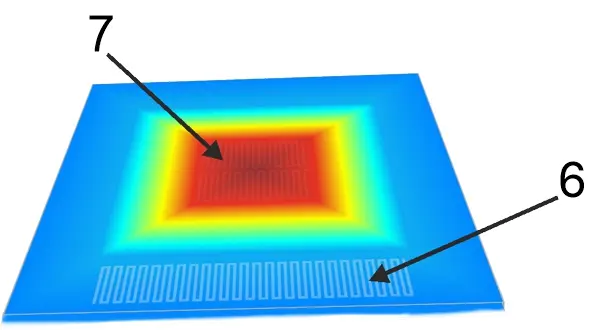
As illustrated in figure 2 a secondary resistive element (7) can be deposited on the MEMS sensor structure and operated to measure the ambient temperature independent of the gas pressure. The temperature measurement is used to compensate the pressure and temperature dependent filament (6).
MEMS Pirani Transducer Advantages
The ultra-thin metal wire used in a traditional wire Pirani gauge is mechanically sensitive to vibrations that can occur from vacuum pumping systems and G-force shock can cause the wire to break. The small mass of the MEMS Pirani sensor makes it extremely robust to continuous vibrations and mechanical shocks of several hundred Gs.
Compared to suspending an ultra-thin wire in a tube by hand crafting, the manufacturing process of a MEMS sensor device is highly reproducible using well-defined and controlled semiconductor processes.
Using a secondary resistive element made from a resistive material with same temperature coefficient as the heat-loss resistive element and extremely low temperature gradients between the two resistive elements enables temperature compensation for measurement drift to a level that cannot be achieved with a wire Pirani design.
MEMS Pirani Process Compatibility
The traditional MEMS Pirani is made of silicon materials and, consequently, is not compatible with aggressive etch process gases such as hydrofluoric acid, which is commonly used in the semiconductor industry. However, recently, new advanced conformal coating techniques have introduced a paradigm shift in MEMS Pirani sensor technology that enable use in aggressive vacuum applications. The coating acts as an efficient barrier against aggressive gases and protects the sensor materials.
Deposition and condensation of materials on the MEMS sensor diaphragm can contribute to a shift in calibration. However, the integration of a special baffle design in the transducer vacuum flange has been demonstrated to be an efficient way to block macroscopic particulates from reaching and damaging the Pirani sensor element. Such particulates often occur in physical vapor deposition applications, also commonly known as PVD applications, or in industrial furnace heat treatment.
The Pirani gauge measures pressure indirectly by measuring heat loss, and consequently, the measurement is dependent on the heat conductance properties of the gas. Modern Pirani vacuum transducers can mathematically compensate with gas correction factors for common gases if the user changes the compensation settings of the transducer.
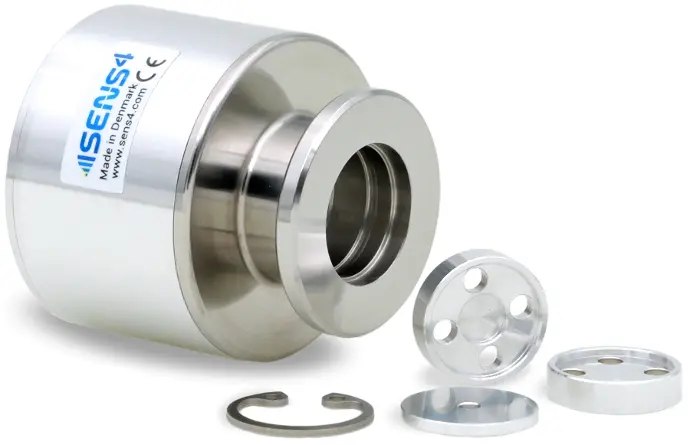
MEMS Pirani transducer with baffle protection from Sens4
Innovation in MEMS Pirani Gauge Technology
The MEMS Pirani can be operated in a balanced Wheatstone bridge; however, the individual components in the bridge circuit contribute multiple temperature coefficient factors, which altogether lead to measurement drift, instability, and noise. Consequently, the Wheatstone bridge circuit is not a practical design for achieving high performance, and legacy electrical circuits have been replaced by advanced signal and data processing.
MEMS Pirani Vacuum Gauge
Recent innovation in MEMS Pirani gauge technology has demonstrated a new and patent-pending technology that combines novel MEMS sensor design with an innovative approach to operating a MEMS Pirani vacuum sensor. The SmartPirani™ technology developed by the Danish technology company Sens4 eliminates the traditional Pirani Wheatstone bridge circuit through the use of advanced precision digital signal processing. The digital approach to temperature compensation and the conversion of heat-loss measurements to a calibrated vacuum gas pressure reading has proven to enhance measurement performance compared to legacy Pirani sensor operation.
The SmartPirani™ technology establishes new performance standards for heat-loss vacuum measurements by extending the dynamic measurement range down to 1.0E-6 mbar (7.5E-7 Torr), which is 2–3 decades lower than legacy wire and MEMS Pirani gauges. Furthermore, this next-generation MEMS Pirani transducer offers improved measurement stability to variations in ambient temperature and has ultra-low measurement noise.
MEMS Pirani Gauge Applications
In general, MEMS Pirani gauges can be performance upgrades to legacy wire Pirani gauges in most vacuum applications and with optional conformal sensor coating also applications where the gauge is exposed to corrosive gases. However, analytical equipment with integrated vacuum systems like mass spectrometers and scanning electron microscopes has several obvious advantages by using MEMS Pirani gauges. The wide measurement range of the MEMS Pirani transducer can in some types of analytical equipment eliminate the need for high vacuum gauges like cold or hot cathode ionization gauges. Ionization gauges are to be avoided in analytical applications where magnetic stray fields, generation of ions and regular maintenance is generally undesirable. Furthermore, ionization gauges are expensive compared to Pirani gauges.
The small geometric size of the MEMS Pirani sensor makes it easy for system integration in equipment where the space is tight. The power required to operate a hot MEMS Pirani resistive filament is very low power compared to a legacy wire Pirani sensor, which makes the MEMS Pirani a smart choice for use in portable battery powered equipment.
Discussion
The heat-loss Pirani vacuum gauge is the most used vacuum gauge in the vacuum industry, and it had earned its popularity because of a wide dynamic measurement range, robustness and low cost. A MEMS Pirani sensor is a mechanically robust solid structure and therefore it has less tendency to shift in sensitivity and zero point.
The vacuum industry has always strived to extend the dynamic range of vacuum gauges to minimize vacuum system complexity and cost of gauges. The SmartPirani™ technology represents a quantum leap in the usable measurement range for the heat-loss vacuum gauge and any further significant measurement range extension in the future is not likely, as the heat-loss measurement principle has reached a physical limit.
The MEMS Pirani technology has been used in many types of vacuum applications for more than 20 years and proven to be reliable and robust. There is no single vacuum gauge type in the market that is the right choice for all applications, and the MEMS Pirani is not compatible with all applications. However, in many industrial and scientific vacuum applications, next-generation MEMS Pirani like the SmartPirani™ will expand to several applications, because the measurement range has been extended into the range dominated by cold and hot cathode ionization vacuum gauges.